Posts Tagged ‘Product Design’
Engineering your way out of the recession
Like you, I have been thinking a lot about the recession. We all want to know how to move ourselves to the other side, where things are somewhat normal (the old normal, not the new one). Like usual, my mind immediately goes to products. To me, having the right products is vital to pulling ourselves out of this thing. There is nothing novel in this thinking; I think we all agree that products are important. But, there are two follow-on questions that are important. First, what makes products “right” to move you quickly to the other side? Second, do you have the capability to engineer the “right” products?
The first question – what makes products “right” for these times? Capacity is important to understanding what makes products right. Capacity utilization is at record lows with most industries suffering from a significant capacity glut. With decreased sales and idle machines, customers are no longer interested in products that improve productivity of their existing product lines because they can simply run their idle machines more. And, they are not interested in buying more capacity (your products) at a reduced price. They will simply run their idle machines more. You can’t offer an improvement of your same old product that enables customers to make their same old products a bit faster and you can’t offer them your same old products at a lower price. However, you can sell them products that enable them to capture business they currently do not have. For example, enable them to manufacture products that their idle machines CANNOT make at all. To do that means your new products must do something radically different than before; they must have radically improved functionality or radically new features. This is what makes products right for these times.
On to the second question – do you have the capability to engineer the right products? Read the rest of this entry »
Part Cutters – Design for assembly dramatically reduces complexity of plasma arc cutter, Joseph Ogando, Senior Editor, Design News
The engineers at Hypertherm Inc., a maker of plasma cutting systems,know a thing or two about cutting metals. They also know how to cut cost. A lot of cost. While redesigning one of the company’s best-selling plasma cutting systems, they managed to reduce parts’ count from more than 1,000 components to fewer than 500. System assembly time fell from 20 hours to less than five. And the output from the company’s existing assembly operation quadrupled — without any additional floor space or an expensive second shift. Bottom line: the redesign saved the company about $5 million in assembly costs over the past 24 months alone, according to Engineering Manager Mike Shipulski. Read the rest of this entry »
Redesigns get radical improvements using DFMA
Redesigns get radical improvements using DFMA
Hypertherm, Inc. of Hanover, NH, is among the world’s foremost manufacturers of plasma arc cutting equipment. Founded in 1968 with a staff of two, the company today has 750 employees, with subsidiaries, sales offices, and distributors in multiple countries. All technology development, product development, and manufacturing is done in the Hanover area.
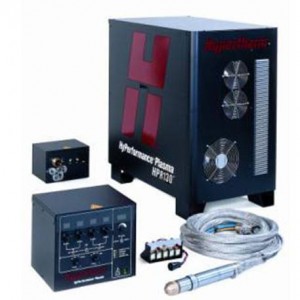
View of the new HyPerformance Plasma HPR130 plasma cutter from Hypertherm. The company used Design for Manufacture and Analysis (DFMA) methodology to radically redesign — and improve — the system’s manufacturability. In the new plasma cutter, system subassemblies took 45% to 89% less time to put together. Assembly floor space opened up by 40%. Warranty cost went down 83%. Cost savings amounted to $5 million over 24 months, which helped the company achieve record earnings and its highest profit sharing on record.
Hypertherm’s products range from lightweight, manual plasma cutting equipment to highly mechanized systems that operate with CNC cutting machines. Its advanced technology serves a global customer base in every industry that depends on quality and reliability in high-temperature metal cutting, such as shipbuilding, construction, farm equipment, rail car and truck manufacture, and plant maintenance.
Recently, Hypertherm engineers tackled a project of mammoth proportions when they remodeled the company’s highly successful HD3070 plasma cutting system — and ultimately created the new HyPerformance Plasma HPR130 plasma cutter. Before the redesign project, the HD3070 sold well and was widely regarded as a standard for robust, high-precision cutting in the industry. Hypertherm wanted to make the product even better.
“We started with a vision to make a radical improvement in product performance coupled with a radical reduction in product cost,” says Mike Shipulski, director of engineering for Hypertherm. He believed that using the methodology of Design for Manufacture and Analysis (DFMA) would help identify unnecessary parts, highlight assembly difficulties that Read the rest of this entry »