Redesigns get radical improvements using DFMA
Redesigns get radical improvements using DFMA
Hypertherm, Inc. of Hanover, NH, is among the world’s foremost manufacturers of plasma arc cutting equipment. Founded in 1968 with a staff of two, the company today has 750 employees, with subsidiaries, sales offices, and distributors in multiple countries. All technology development, product development, and manufacturing is done in the Hanover area.
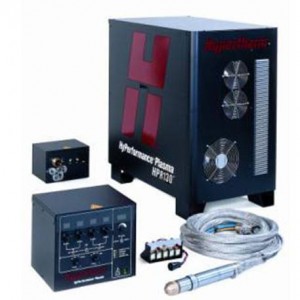
View of the new HyPerformance Plasma HPR130 plasma cutter from Hypertherm. The company used Design for Manufacture and Analysis (DFMA) methodology to radically redesign — and improve — the system’s manufacturability. In the new plasma cutter, system subassemblies took 45% to 89% less time to put together. Assembly floor space opened up by 40%. Warranty cost went down 83%. Cost savings amounted to $5 million over 24 months, which helped the company achieve record earnings and its highest profit sharing on record.
Hypertherm’s products range from lightweight, manual plasma cutting equipment to highly mechanized systems that operate with CNC cutting machines. Its advanced technology serves a global customer base in every industry that depends on quality and reliability in high-temperature metal cutting, such as shipbuilding, construction, farm equipment, rail car and truck manufacture, and plant maintenance.
Recently, Hypertherm engineers tackled a project of mammoth proportions when they remodeled the company’s highly successful HD3070 plasma cutting system — and ultimately created the new HyPerformance Plasma HPR130 plasma cutter. Before the redesign project, the HD3070 sold well and was widely regarded as a standard for robust, high-precision cutting in the industry. Hypertherm wanted to make the product even better.
“We started with a vision to make a radical improvement in product performance coupled with a radical reduction in product cost,” says Mike Shipulski, director of engineering for Hypertherm. He believed that using the methodology of Design for Manufacture and Analysis (DFMA) would help identify unnecessary parts, highlight assembly difficulties that hampered throughput, and pinpoint costs that didn’t support performance. “We set explicit cost and performance goals for the redesign project,” he says, “and DFMA analysis helped us achieve them.”
Adventures in assembly
Plasma cutters essentially consist of a power supply unit, a torch assembly, and a gas selection and metering console. When the machine is switched on, current flows from an electrode in the torch assembly to the workpiece. An electric arc is created, which superheats a surrounding stream of cutting gas. The heat turns the gas to plasma. The hot plasma exits the torch through a nozzle and is directed by a second stream of shielding gas to make controlled cuts in steel plate or other metals on the worktable.
The HD3070 redesign project was Hypertherm’s first large-scale venture into DFMA. The first step in redesign was to benchmark a product called the HT2000, which the production team considered the easiest system to assemble. Shipulski assigned mechanical applications designers Brian Currier and Rick Anderson the task of counting all the parts in the HT2000 and sent them out onto the shop floor with pencil and paper. As a guide to the correct analysis methodology, he gave the engineers his well-thumbed copy of the “Boothroyd Dewhurst Design for Assembly” handbook. Their job was to build a production version of the HT2000, their simplest power supply unit, and see how long it took.
“As designers, we had never done such a thing,” says Currier. “The product had 1,000 parts. After spending a week on the floor, building one of these units, we were really motivated to improve the design so it was easier to assemble.”
“They came back with a Pareto chart of part count by type, and roughly two-thirds of the parts were fasteners and connectors,” says Shipulski. “That gave them a real gut feeling about what was driving assembly time and cost for the product. Looking at CAD models and drawings is different than assembling something that’s impossible to put together easily,” he continues. “A hands-on understanding is important. You have your knuckles skinned; you can’t fit the tools in. You sit there, listening to the sound of nut runners securing parts, and you begin to get ideas about redesign.”
The kindest cuts
Currier and Anderson zeroed in on the main cost drivers for the HT2000 plasma system. The power supply unit required assembly from all four sides. It included a lot of extra sheet metal. Each subassembly in the power supply involved too many fastening and connecting operations, as did the separate automatic gas console they benchmarked.
One of the first things we did,” says Anderson, “is we brought in our sheet metal suppliers and asked, how can we do this better? They gave us great ideas about how to incorporate mounting tabs and alignment features into the design.”
Before starting design work for the HPR130 power supply, Hypertherm benchmarked an existing power supply unit using DFMA methodology. This view shows only the left side of the HT2000 benchmark unit. It has 1,000 parts and is assembled from all four sides. Assembly time is 10 hours.
View of Hypertherm’s redesigned HPR130 power supply. It has about 500 parts and is assembled from two sides — in 63% less time. Hypertherm engineers improved assembly efficiency by incorporating mounting tabs and alignment features into the sheet metal structure, by simplifying cable connections, and by replacing dozens of wire connections with new printed circuit board designs.
Hypertherm also challenged its own electronics experts to replace dozens of separate wire connections with new printed circuit board designs. As Currier and Anderson divvied up the subassemblies, a design theme emerged. “For electrical wiring or connecting, we’d try to do them on the board if we could,” says Shipulski. “For gas, pneumatic, or water connections, we’d try to do as few as possible or with as few parts as possible.”
The original pilot arc controller subassembly had 88 parts. Anderson’s economical new version has only 16. Anderson also reworked the AC-to-DC converter (nicknamed the “chopper”), nearly halving assembly time and saving Hypertherm over $200,000 a year
View of the pilot arc controller, which is a subassembly in the power supply unit. The original subassembly (left) had 88 parts. For the redesign (right), Hypertherm engineers cut the number of parts to 16.
View of the AC-to-DC converter, another subassembly in the power supply. The original subassembly (left) had 73 parts. The new design (right) has only 47 parts and can be assembled in about half the time. Redesign of this subassembly alone saved Hypertherm over $200,000 per year.
Currier completely rethought the design of the automatic gas console. The original console had one large, complex manifold that was laboriously assembled on a cart that rolled through the factory. The new console has four small, simplified manifolds, and each can be built on a benchtop. Pre-cut, color-coded tubing with push-to-connect fittings avoids the need for time-consuming sealant. Part count for the console went down by 63% — and assembly time by an amazing 90%.
Hypertherm also redesigned a standalone automatic gas console, which meters and delivers gas for plasma cutting. The original console used as a benchmark for DFMA analysis (center) was a single, large device. In the redesign (left and right), Hypertherm engineers split the console into two smaller units that could be assembled more efficiently.
Close view of the redesigned two-part automatic gas console for the HPR130 plasma cutter. Even with added functionality, part count went down by 63%, and assembly labor time plummeted 90%.
When Currier and Anderson were done, fully half of those 1,000 parts were history. In the new plasma cutter, called the HPR130, system subassemblies took 45% to 89% less time to put together. Assembly floor space opened up by 40%. Warranty cost went down 83%. Cost savings amounted to $5 million over 24 months, which helped the company achieve record earnings and its highest profit sharing on record. A new modular design approach enabled standardization across the entire product family, promising further savings down the road.
“This project showed everyone in our company how improving assembly sequence saves cost and reduces defect opportunities,” says Shipulski. “Hypertherm has a DFMA mindset now. We use more alignment features and fewer fasteners and connectors. We benchmark existing products for part count and assembly time. We score designs using real numbers, so design comparisons are straightforward and credible.”
With the success of its radical redesign project freshly in mind, Hypertherm saw the value of extending the practice of assembly analysis across multiple product lines. To support this initiative, the company purchased DFMA software from Boothroyd Dewhurst, Inc. of Wakefield, RI. The software guides engineers through the steps in analyzing products for assembly simplification and then estimates the cost of manufacturing new designs.
“The results we got from using the handbook showed how an investment in the software would pay off,” Shipulski says. “The basic approach to doing DFMA is the same. The engineers go out and build the existing product. Then they use the software to score the baseline design and review opportunities for reducing assembly time.”
DFMA software gives Hypertherm a standardized reporting format for comparing analyses performed by different engineering teams. It also supports analysis at a high level of detail. “When we first started doing DFMA, we didn’t have the software, so we had a lot of debates about how to score assembly operations,” says Anderson. “The software helps avoid that. Now we can all score the same assembly and come up with similar numbers.”
Currier is presently using DFMA software to guide the redesign of a torch for a brand new plasma cutting system under development. The primary components of the torch are two current-carrying parts, separated by an insulator. The original design included a manufacturing operation that added hours to the build time, so Hypertherm targeted that operation for elimination.
Hypertherm used DFMA software to analyze and simplify the design of a plasma cutting torch. An exploded model of the original torch assembly is shown at top. For the new torch design (below), Hypertherm engineers determined how to configure adjacent copper tubing without requiring Teflon insulating sleeves. They saved additional cost by eliminating a time-consuming potting process. Part count for the torch fell from 58 to 42. Assembly time dropped from 374 minutes to seven minutes.
The original torch design took more than six hours from start to finish. The new design takes less than 10 minutes.
“One of the features I like about the DFMA software is being able to add assembly operations that specify the way we do things,” says Currier. “Our current brazing methods didn’t really match the software, so I just went out with a stopwatch, timed people doing a braze step, and re-created the operation using our data. Now when I need to put a braze joint into a torch analysis, I can just select it and know it’s applied consistently across every design.”